Building Envelope Commissioning: A Game-Changer for Sustainable and High-Performance Buildings
- Octavian Vasilovici
- Dec 31, 2024
- 4 min read
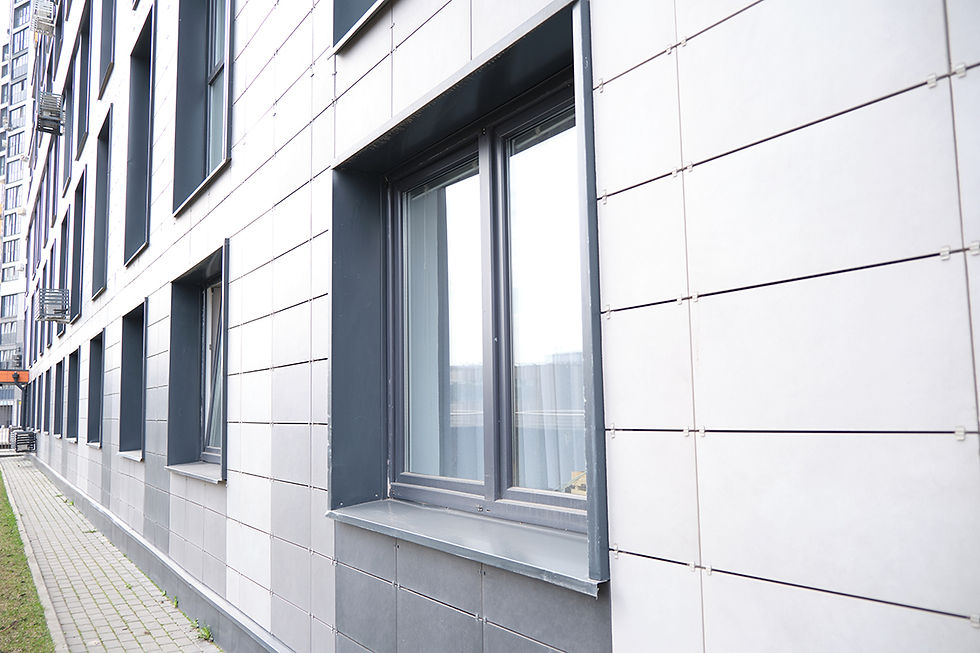
As construction standards evolve and sustainability becomes a global priority, Building Envelope Commissioning (BECx) has emerged as a cornerstone of modern building practices. More than just a technical protocol, BECx ensures the building envelope performs as the first and most critical barrier against inefficiencies in energy, durability, and occupant comfort.
With the building envelope representing the largest interface between interior and exterior environments, BECx directly impacts a structure’s thermal comfort, HVAC performance, and operational costs. It’s not just about building to code; it’s about building smarter, more durable, and future-ready structures.
What Is Building Envelope Commissioning?
BECx is a rigorous, multi-phase process that guarantees a building’s envelope—the barrier between interior and exterior environments—delivers on key performance metrics. These include thermal resistance, air and water tightness, and durability. By safeguarding against inefficiencies, BECx reduces energy waste, improves HVAC system performance, and extends the life of the building.
Why Is BECx More Relevant Than Ever?
Increased focus on sustainability and green building certifications such as LEED and Passive House has amplified the importance of BECx. A well-commissioned building envelope directly contributes to these certifications by minimizing energy consumption and reducing carbon footprints.
Additionally, the rise of carbon reduction governmental mandates has placed BECx in the spotlight. "The envelope is no longer just a passive component", says Octavian Vasilovici, Principal OptiBuild Consulting Engineers. “It’s an active part of achieving optimal performance and resiliency. Without a properly commissioned envelope, even the most advanced HVAC systems struggle to perform efficiently.”
Key Phases of BECx
BECx unfolds in four distinct phases, each with specific objectives:
1. Planning Phase
Owner’s Project Requirements (OPR): Establish performance benchmarks for thermal resistance, air tightness, water resistance, and durability.
Design Intent Document (DID): Convert OPR into actionable design guidelines.
BECx Plan: Define the scope, responsibilities, and methods for implementation.
2. Design Phase
Design Reviews: Verify that the proposed designs align with OPR and industry best practices.
Material and System Selection: Ensure chosen materials meet the required specifications.
Mock-Ups: Construct and test full-scale sections to validate constructability and performance.
3. Construction Phase
Pre-Installation Meetings: Coordinate among trades to prevent conflicts during installation.
Onsite Inspections: Verify installations match designs and specifications.
Functional Performance Testing: Conduct air tightness, water penetration, and thermal performance tests (e.g., blower door tests, infrared thermography).
4. Post-Construction and Operations Phase
Documentation: Compile comprehensive reports detailing compliance and test results.
Training and Handover: Educate building operators on maintaining envelope performance.
Monitoring Plan: Provide recommendations for ongoing performance assessments through tools like sensors and inspection schedules.
Who’s Involved in BECx?
Effective BECx demands collaboration across multiple disciplines. Key stakeholders include:
Building Owners: Define envelope performance goals and allocate resources.
Commissioning Authority (CxA): Lead the BECx process, ensuring compliance and providing third-party validation.
Architects: Develop performance-driven designs while coordinating with structural and mechanical systems.
Structural Engineers: Ensure envelope systems account for wind loads, thermal expansion, and integration with structural frameworks.
Envelope Specialists: Focus on materials, thermal performance, and system detailing.
Contractors and Subcontractors: Execute envelope construction and participate in quality assurance processes.
Testing Agencies: Conduct performance evaluations like air leakage and water penetration tests.
HVAC Engineers: Align envelope performance with mechanical systems to optimize energy efficiency.
Building Operators: Maintain the envelope’s integrity post-occupancy.
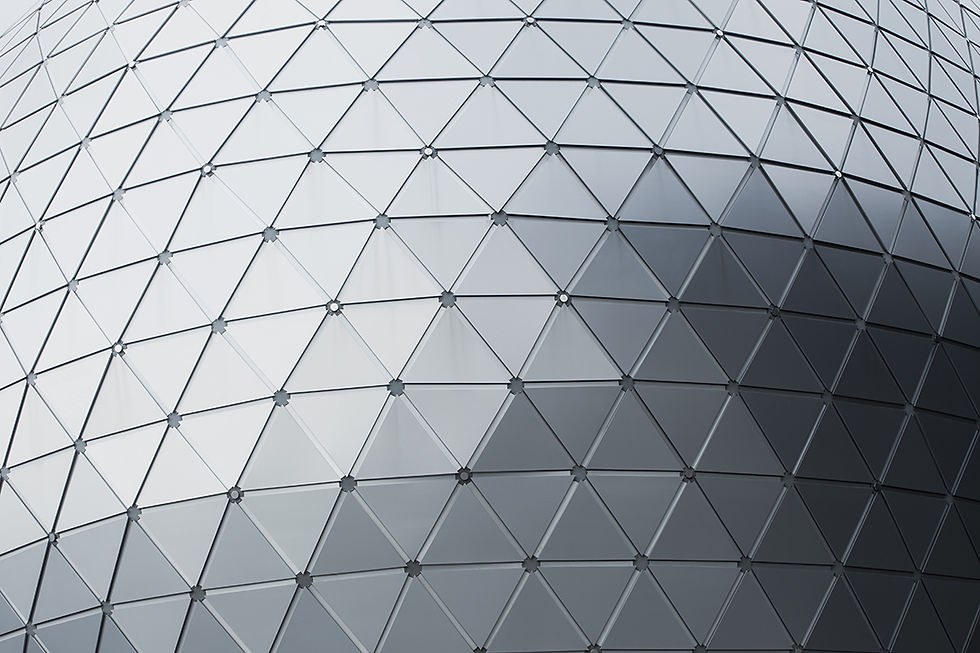
Why Is BECx Essential?
The building envelope directly impacts HVAC performance and operational efficiency, making BECx a critical step. Key benefits include:
Thermal Resistance: Proper insulation reduces heat transfer.
Air Tightness: Limits air infiltration/exfiltration, stabilizing indoor environments and reducing energy loads.
Moisture Control: Prevents condensation and structural damage.
Durability: Enhances long-term performance and minimizes repair costs.
Commissioning the building envelope leads to optimized HVAC performance, improved energy efficiency, and greater occupant comfort.
Trends Shaping the Future of BECx
The importance of BECx has only grown in light of emerging trends in construction and sustainability:
Green Building Certifications
With programs like LEED, Passive House and Green Globes prioritizing envelope performance, BECx is often a prerequisite for certification. Proper commissioning directly contributes to energy efficiency, occupant health, and carbon reduction goals.
Carbon Neutral Ready Buildings
Carbon reduction goals hinge on minimizing energy loss, making BECx a pivotal part of the design strategy. A commissioned envelope can significantly reduce HVAC demands, paving the way for carbon-neutral buildings.
Integration of Advanced Technologies
BECx now leverages digital tools like Building Information Modeling (BIM), drones, and AI for enhanced accuracy. These technologies streamline the design-review process and provide real-time insights during testing and monitoring phases.
Why Is Early Involvement Key?
Engaging a Commissioning Authority (CxA) during the conceptual or early design phase ensures seamless integration of BECx into the project. Early involvement allows the CxA to:
Prevent Costly Rework: Identifying potential issues early minimizes expensive construction-phase fixes.
Align Goals Across Teams: Facilitates a shared understanding of performance requirements among all stakeholders.
Enhance Efficiency: Testing and mock-ups during design reduce risks of post-occupancy failures.
Support System Integration: Early collaboration ensures the envelope complements MEP and structural systems.
BECx: Supporting a Sustainable Future
As the construction industry continues to prioritize sustainability and operational efficiency, Building Envelope Commissioning emerges as a cornerstone of high-performance buildings. By ensuring that the envelope performs as intended, BECx reduces energy consumption, optimizes HVAC systems, and supports green certifications—all while providing superior indoor comfort.
“At the end of the day, BECx isn’t just a best practice—it’s a necessity for anyone serious about building performance and environmental responsibility,” concludes Octavian Vasilovici.
Contact us today to learn how we can support your next project!